“Steps in the right direction”
An interview with Magnus Schmid, the person at the German Partnership for Sustainable Textiles who is responsible for implementing its goals.
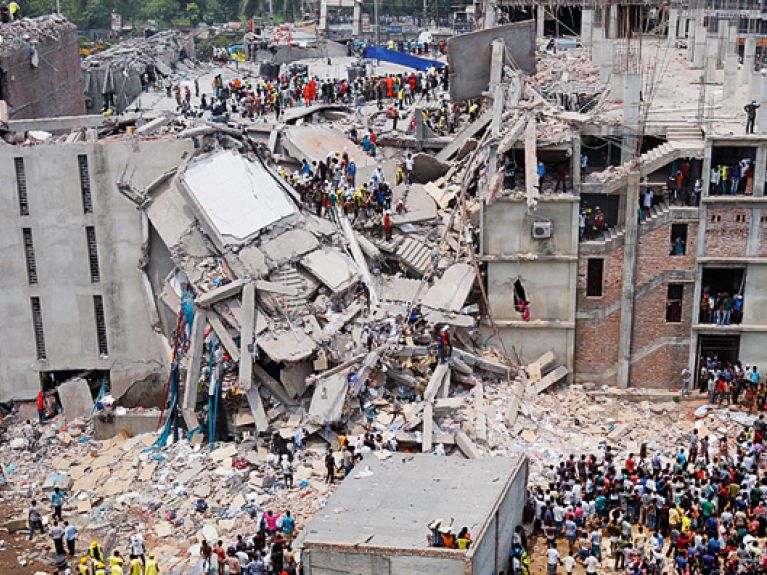
Mr Schmid, you were in Bangladesh when the textile factory there collapsed in 2013. What did you do there at the time – how did you respond?
Between 2011 and 2015, I led a project supporting the textile industry in Bangladesh for the Gesellschaft für Internationale Zusammenarbeit (GIZ). Working on behalf of the Federal Government, we were assisting factories to introduce better working conditions and environmental standards and helping the Government of Bangladesh to train labour inspectors. At about 9 am on 24 April 2013, we heard that an eight-storey building with five factories in the suburb of Savar had collapsed and there were already eight deaths. No one suspected at this point that there would be over 1,100 people killed and 3,000 injured in this disaster. In the first instance, we provided very practical help. The emergency workers urgently needed water, food and torches, which we obtained from nearby supermarkets. In the days that followed, our project supported local hospitals with medicines, blankets and meals. Together with non-governmental organisations and the International Labour Organization (ILO), we opened drop-in centres for relatives of the Rana Plaza victims. We provided artificial limbs for the injured and training in small business ownership for about 500 men and women who were no longer able to work in large factories because of the trauma they had suffered. Today these people are working as local tailors and greengrocers or running restaurants.
The textiles partnership was formed in Germany in 2014 as a result of the devastating accident. Who is involved in this group and what is its objective?
In 2014, Gerd Müller, Federal Minister for Economic Cooperation and Development, invited various stakeholders to form a round table, from which the Partnership for Sustainable Textiles then developed. It included representatives from the textile industry, civil society and trade unions, along with a number of Federal Ministers. Our objective is to work together to improve social, economic and environmental conditions along the entire textile supply chain. To this end, the members pool their expertise, use synergies in the manufacturing countries and learn from one another. Higher pay and living wages for workers along with safer workplaces are among the goals of the textiles partnership. This means specifically, for example, ensuring clean drinking water, noise or dust protection at the workplace, adequate fire escapes, safe buildings and safe handling of chemicals.
You have been in charge of implementation within the partnership since the start of the year. What does this mean in specific terms?
Since last year, the members of the textiles partnership have met in working groups to discuss the social and environmental demands that partnership members must implement in future. The working group for implementation and internationalisation began its work in February 2016. Its task is first of all to begin broad joint initiatives for the exemplary implementation of the partnership’s objectives. At the partnership secretariat, we coordinate the meetings, make the conclusions available to all and support future practical initiatives from planning through to implementation. We are thinking here, for example, of training for local advisors, who educate manufacturing companies in occupational safety and fire prevention and chemicals management, or courses of further training to allow women to take on management roles. The working group on implementation has set itself the goal of developing and carrying out its initiatives in close coordination with manufacturing companies, public and civil society actors locally and international organisations, such as the ILO.
Apparently there is a game that is used to train female workers. What is it and what has the feedback been?
We have worked with non-governmental organisations in Bangladesh to set up 19 women’s cafes for workers. The trainers are specialists in national labour law. They make the women aware of their rights and prepare them for negotiations with factory management. Common areas of dispute between employers and female workers are irregularities in the payment of overtime or unlawful dismissal of workers (both men and women). We expanded on the board game of Ludo to give some very practical tips here. Players draw cards with questions on labour law in Bangladesh. If they know the answer, they can throw the dice and move their piece forward. The game is popular, and there are even annual Ludo championships, with teams from the various women’s cafes competing against one another.
Approximately four million people in Bangladesh work in roughly 5,000 textiles factories. What are your achievements to date?
The Federal Ministry for Economic Cooperation and Development (BMZ) has been promoting the improvement of social and environmental standards in Bangladesh for a long time. In addition to the programme to promote social and environmental standards, German development cooperation is also supporting Bangladesh in the introduction of an accident insurance scheme for the textile and leather sector. Together with the EU and the French Development Agency (AFD), we are providing a credit line and advisory measures for companies that are prepared to invest in the modernisation of their plants and improvements in safety. With a regional programme, German development cooperation is also supporting the entrenchment of social and environmental standards in the entire region.
We work alongside government organisations, the private sector and civil society. The project has advised more than 780 factories on the improvement of social and environmental standards since 2010. To this end, first we provided training to teams of advisors in the employer associations and from local consulting firms. We set up courses for the middle management of factories at state and private technical colleges. We have reached about 100,000 factory workers through the women’s cafes. Together with the ILO, the project is currently training 300 labour inspectors, who will in future guarantee that labour law is implemented. In addition, for example, fire services have been set up in the factories, a training programme has been developed for factory workers to operate water treatment plants, and solutions have been introduced for disposal of sewage sludge containing heavy metals.
What is the incentive for firms in Bangladesh to cooperate with you?
Pressure has grown on international buyers and local manufacturing companies to improve occupational safety and fire protection and to improve working conditions in factories. The pictures of the fire in the Tazreen Fashion factory in 2012 with over 100 deaths and the collapse of Rana Plaza in 2013 with over 1,100 deaths have still not been forgotten. This really brought home to consumers the suffering of people involved in textile production. There has been a new awareness because it is clear that “my own clothes are also made in factories like that”. More and more firms now recognise that investment in improving working conditions and protecting the environment pay off in the long term and support economic success.
What is the timeframe for this project? Can you tell us a positive example or something which you have particularly enjoyed in your project work?
The project in Bangladesh is initially set to continue until mid-2017. I am proud of a decree that the Minister for the Environment signed at our initiative on the disposal of industrial sludge. Factories must in future dispose of such waste appropriately. This is real progress. I was moved by conversations I had with victims of the Rana Plaza collapse, women who in many cases had to wait several hours or even days under the ruins of the building until they were saved. There is one woman I remember particularly: Shirin Akter. The 25-year-old worker was on the fourth floor when the building collapsed. She lost both legs during the rescue and had several operations in hospital. After nine months she stood up again for the first time on prosthetics. We gave her back hope. The orthopaedic technicians for the manufacture of the simple prosthetics were also trained through our project.
Interview: Martin Orth