Smart Factory
Researchers have built a “factory of the future” in an unassuming hall in Kaiserslautern.
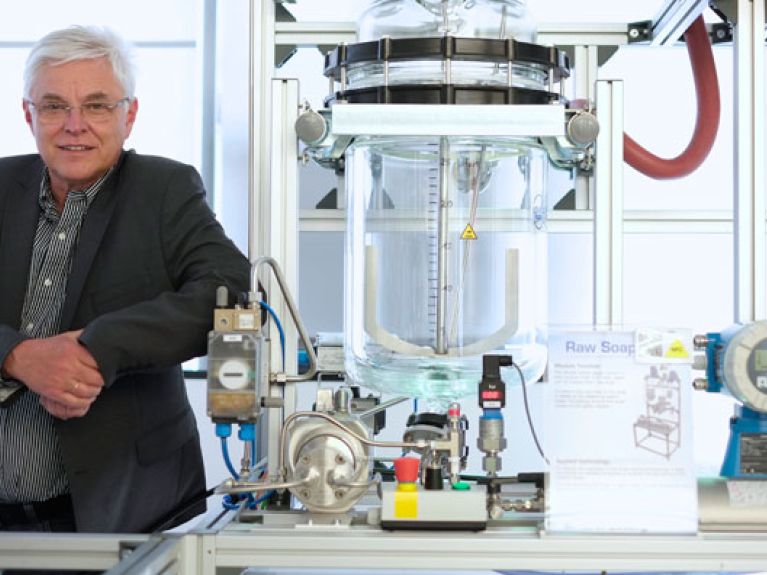
Detlef Zühlke doesn’t look much like a revolutionary as he stands there in the small production hall. The professor is wearing a jacket and rimless glasses, and his left hand is playing with a Lego brick. Around him hang countless tubes and cables that look so new and clean that they must still be waiting for their first big job. To a certain extent that is also true. They form part of a model factory of the future that Zühlke has set up here at the German Research Center for Artificial Intelligence (DFKI) in Kaiserslautern. The idea of the Smart Factory is considered a major element of the fourth industrial revolution.
The story of the factory of the future in Kaiserslautern began during a train journey. Zühlke was on his way home from Duisburg, where the researcher had visited a Fraunhofer-Gesellschaft prototype building. It was a residential house packed with special energy-saving solutions and intelligent devices. Full of impressions after a long and interesting day, Zühlke’s mind wandered back to the “smart home” and then in other directions. Why shouldn’t what was possible in homes also be possible in factories? If it were possible to digitally network devices for optimized processes to satisfy the personal wishes of residents, couldn’t the same be done for customers? “We need a prototype,” thought Zühlke. He thought over the idea for a few weeks and eventually asked people in industry what they thought of it.
The facility in Kaiserslautern shows just how positively the proposal was received. Everywhere parts have been installed from companies that today belong to the association behind the Smart Factory. Yet, despite backing from industry, it turned out to be a difficult start. Even visionaries have to comply with red tape. Zühlke and his supporters discovered that when they considered what kind of product their test plant could make. “It had to be simple, have novelty value and inspire people.” A biscuit manufacturer offered his support, and the production of spirits was also proposed. Ultimately, however, because of the strict regulations governing food production, a clean solution was chosen: soap.
Three containers of liquid hang like infusion bags over the production line. Tubes run down to the conveyor belt that transports the empty plastic bottles which are filled with soap. So far there’s nothing particularly spectacular about that. The difference between the Smart Factory and a conventional production plant is concealed in the rectangular stickers on the backs of the plastic bottles – computer chips. The staff here call these “product memory”. “The product carries its own information and tells the machine how it is supposed to turn out,” explains Dr. Matthias Loskyll, Deputy Research Director at the Smart Factory. Must the bottle be filled with blue, red or yellow soap? Or a blend of soaps? If so, what are the proportions? Should a black, white or grey top be put on the bottle? What should the label say? This soap factory looks simple, but the variety of products it can produce is infinite.
That is the goal of the Smart Factory: complete flexibility at the highest possible speed. “We need to better reflect our increasingly rapidly changing world,” says Zühlke. His dream is that a customer orders a product on the Internet and production immediately begins in the factory according to his or her personal wishes – and without having to change the production line. If machines do need to be changed, then this should occur on the basis of the “plug and play” principle: everything is compatible with everything else. It should be possible to take a factory apart and put it back together again just as easily as a pile of Lego bricks. To illustrate this Zühlke and his staff developed another production line and exhibited it at the 2013 Hanover Fair. It produces small flashlights with a personal engraving, but can also produce key finders, special key rings that owners can find with the aid of a mobile phone. Each machine in the production process can be unplugged and replaced in a matter of seconds. Instead of a central control system, each component has its own tiny computer.
That looks less futuristic that it sounds – particularly as there is a sign hanging on a table immediately adjacent to it with the inscription “Manual Work Area”. Will that still be required in the future? “Definitely,” replies Loskyll. “Especially in the automotive industry there will continue to be tasks that need to be done by hand.” In the future, however, even the manual work and training involved will be carried out in a “smart” way. The manual workplace of the future will combine working on real objects with three-dimensional models. “Augmented reality” is the buzzword here. A video camera looks down on the table from above. The image appears on a monitor and the worker can see his own hands as they perform an intricate assembly task. Animations along the upper edge of the screen show him what to do next – step by step.
“Human beings will still have a place in the Smart Factory,” says Zühlke. And they will by no means only perform remaining manual tasks. “It’s all about flexibility, and the human being is the most flexible element in the whole system. He or she will be the problem solver who walks around the factory and checks that everything is working.” However, that would involve a new form of training. Zühlke argues that the often rigid boundaries between occupations and academic disciplines should be opened up. He actually studied electrical engineering, but completed a doctorate in mechanical engineering. “Eventually I noticed that what we’re doing here is meaningless without computer science.” Today he is in charge of the Chair of Production Automation at Kaiserslautern University of Technology. His career has followed the Lego principle on which the Smart Factory is also based.
The building that houses the factory has a large glass facade. Zühlke has made sure that the production facility is brightly lit at night – as a show window for students at the nearby university, who pass by on their way into town. The professor wants to attract people and make them curious. In his opinion, the shortage of young researchers who are well prepared for Industry 4.0 is one of the three reasons why the Smart Factory has not yet become a reality. The second reason is a lack of common standards. Lego bricks fit together without any problems because they all come from the same manufacturer. That does not apply to machines. Production processes must become “manufacturer-independent” – yet another term that is frequently heard at the Smart Factory. The third unresolved question is security. How vulnerable is this new industrial world? How can you protect a system that is based on transparency and interchangeability against sabotage? How can you guarantee data protection when computer chips log absolutely everything that happens to a product?
“I assume we’ll be able to find solutions,” says Zühlke. “We don’t have any other option.” He is firmly convinced that Industry 4.0 is Germany’s only chance of maintaining its economic position. Although it is still in the lead on the path to the factory of the future, the international interest is great. Zühlke travels a lot. He is regularly invited to report on the progress being made in this modest hall in Kaiserslautern. Enquiries arrive from all over the world, “only Europe is quiet”. Asian countries in particular are taking notice. Korea, for example, is pursuing a similar technology project. The USA, on the other hand, is relying on broad re-industrialization rather than targeted high-tech strategies.
Zühlke is now 64 and he will be retiring at the beginning of 2015. He foresees the first major elements of the Smart Factory being implemented in real industry in three years and a complete factory perhaps in ten. Zühlke wants to be involved when that stage is reached, wants to maintain his links with the project whatever happens. “It would be really sad if you pull up your shirtsleeves, stick your hands deep into engine oil and then suddenly have to drop everything and leave.” ▪