On the pulse of time
The art of watchmaking at Glashütte in Saxony is a story of success. A visit to the Erzgebirge, where traditional craftsmanship meets high technology.
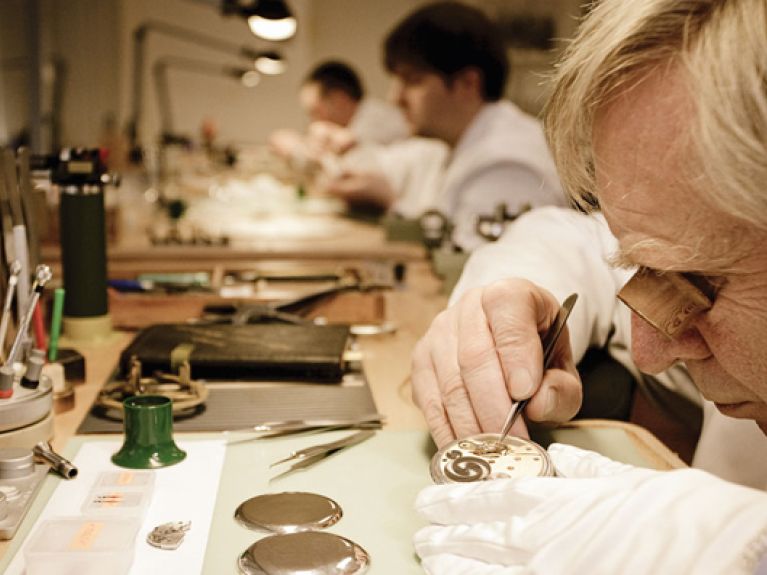
If you want to experience the fascination of time, all you need to do is set off for a rather remote destination. In the Erzgebirge, to the south of Dresden and close to the Czech border, lies Glashütte. State road no. 178 meanders for 15 kilometres through the narrow valley of the River Müglitz before reaching the destination. A sign on the edge of the town announces “Time lives here”, welcoming you to Glashütte in the district of Sächsische Schweiz-Osterzgebirge, or Saxon Switzerland – East Ore Mountains. The town consists of two larger roads lined with attractive facades, a railway station, a supermarket and a savings bank. It is set amidst wooded hills, with names such as Ochsenkopf or Schützenhöhe. But the small provincial town with 7,000 inhabitants has surprisingly close links with the big, wide world: Glashütte is known around the globe for its fine craftsmanship – for the manufacture of the highest precision mechanical watches. An attractive location set in idyllic surroundings.
Stuttgart and its environs characteristically have a large number of companies associated with car manufacturing, a driving force in the regional economy. In Frankfurt am Main the big banks concentrate the expertise of the financial sector and are important employers. In contrast, Glashütte is an eastern German success story with its exceptional timepieces. Here, the outstanding mastership of the watchmaking industry has evolved over more than 165 years. And these skills are concentrated in just a few square kilometres, forming an economic cluster that secures not only competitive advantages and growth prospects for the manufacturers but also important jobs in the region. In Glashütte a dozen watch manufacturers employ a good 1,000 people. Relationships between the companies are good and neighbourly, although they do not work directly with each other. Each brand has its own philosophy and has established its own market niche. In this way they have created a renaissance in the watch industry, 20 years after German reunification. Today, Glashütte again stands for the highest precision, top quality and original design in the watchmaking world. The high level of manufacturing precision – from the smallest screw to the complex movement is the characteristic trademark. At least 50% of the movement has to be produced directly in Glashütte before a watch is able to boast the famous name.
Glashütte is a microcosm of watches and time: a clock face on the town’s coat of arms, the Café Uhrwerk on Hauptstrasse, a tour of the 35 key sites in the past and present of watchmaking, and the impressive German Watch Museum. Opened in 2008, it exhibits around 400 items illustrating the Saxon art of watchmaking. The project was initiated by Nicolas G. Hayek, one-time head of the famous Swiss watch company, Swatch, which also owns the Glashütte Original brand. The fact that someone from Switzerland supported this museum is a sign of recognition for the watchmaking industry in Saxon Switzerland – and for the founding father, Ferdinand Adolph Lange. The town has a memorial to him on the market square. Surrounded by flower beds and benches, it depicts the bust of the man who started the clocks ticking in Glashütte. At the end of 1845 the master watchmaker from Dresden set up his manufactory “Lange&Cie” and laid the foundation stone for precision watchmaking in Glashütte.
Now, in the 21st century, many of his ideals live on in Altenberger Strasse and at Ferdinand-Adolph-Lange-Platz. This is the base of three companies that brought fame to the town: Lange Uhren GmbH with its brand name of A. Lange&Söhne, Glashütte Original and Nomos Glashütte. They are the only manufactories. In order to bear these special names, the movement – the complex internal mechanism of the watch – has to be both developed and crafted by the manufacturers themselves. And this takes time. It can take years before the initial design is finally ready for the market. A. Lange&Söhne currently produces 28 different movements. When making a mechanical watch, between 200 and 600 often miniscule parts have to be assembled in stages. The process involves a great deal of manual craftsmanship as well as some high technology. “That’s the basis of our precision manufacturing,” says Christian Engelbrecht of A. Lange&Söhne as he leads the way into the components hall. It smells of oil, and design blueprints are spread out. Large machines are milling fine contours and boring tiny holes into the circles of metal that form the foundation of each movement – the plate. Next door, in the test room, each contour and bore hole will later be carefully measured using precision techniques. Precision is given top priority with tolerance levels down to the smallest fraction of a human hair.
The fine processing section then provides a deeper insight into the world of the three-quarter plate, blued screws, the anchor and the motion. This is where individual parts of the movement are smoothed, polished, embellished and pre-assembled. A grinding noise, like in the dentist’s surgery, can be heard in the decorative engineering section of A. Lange&Söhne, where a craftswoman is working on a bridge part with a polishing machine. Engraving is a delicate task: she uses a graver to engrave delicate floral patterns on a balance cock, a mounting for the movement, smaller than a fingernail. This is her personal signature that transforms each of the brand’s watches into a unique piece.
The moment when the watch comes to life arrives when the mechanism is assembled. This is the hour of the watchmakers and their craftsmanship. Work on the heart of the timepiece takes place at Nomos Glashütte. The Chronometry Building is located on the Erbenhang, a hillside overlooking the rooftops of the town. This is where 40 watchmakers, almost half of all the staff, assemble the specified designs in small production lines and test their accuracy. The masters of time sit behind doors labelled “Winding Mechanism and Movement Assembly”, “Final Adjustment” and “Complex Processes”, where extremely sophisticated mechanisms are assembled. Their small empire resembles a combination of laboratory and workshop. Wearing white coats bearing a watch logo, they sit at watchmakers’ benches, their chins close to the surface and arms supported to position their tools with the utmost precision. A craftswoman looks through a magnifying glass and uses ultra-fine forceps to gently install the ratchet wheel, then carefully tightens the tiny screw. The people who work here need great patience and diligence, a keen eye and a steady hand. It is these virtues and their specific application that have set Nomos and A. Lange&Söhne on the path to success and generated a small economic miracle in the east.
After the fall of the Wall and reunification in 1989/1990, nobody would have dreamt of this development. When the state-owned company Glashütter Uhrenbetriebe closed, the watchmaking industry lay in ruins. Revival was boosted by the enterprising spirit of men such as Walter Lange. In 1990 the great-grandson of Ferdinand A. Lange founded Lange Uhren GmbH with 470 employees and registered the brand name A. Lange&Söhne. His ambition was for Lange to manufacture the best watches in the world again. Each year only a few thousand watches are produced with this brand name, which now belongs to the Swiss luxury goods group Richemont. “We’re the only German watch brand serving the premium segment of the market, and it stands for first-class quality in more than 50 countries,” says CEO Wilhelm Schmid, who wants to spread the fame of the brand name which already has its own stores in Shanghai, Tokyo and Seoul. The perfection and exclusiveness of A. Lange&Söhne have their price: well-heeled watch lovers now pay six-figure euro sums for ingeniously manufactured timepieces that are made from the finest gold or platinum and represent the pinnacle of manufacturing excellence.
The ambition to create these unique timepieces can also be felt inside the building of the renovated former railway station. Nevertheless, the watches at Nomos Glashütte tick differently. The manufactory has found its own special niche in the market. Roland Schwertner, a business administrator and photographer from Düsseldorf, built the still independent company at the beginning of the 1990s with a great deal of idealism and now works behind the scenes as strategist. The pioneer’s idea, to combine traditional watchmaking techniques and modern design, has made Nomos watches a market success. The clear, simple lines of the watch face, slender hands and fine-gauge lunette: models such as Tangente, reminiscent of the Bauhaus, stand for the brand’s timeless, clear-cut design and are regarded as classics on the wrist. With prices starting at 1,000 euros, they don’t have to cost a fortune. Uwe Ahrendt, born in Glashütte and sole CEO of Nomos since 2010, sees the diversity of the Glashütte companies with their individual approaches as an advantage for this business location. Ahrendt talks about sticking to principles when he looks to the future of his company. “Quality comes before quantity. We don’t want growth at any price,” he says over a coffee in the garden of the Chronometry Building. Nomos sells about 80% of its watches in Germany, and his aim is to extend this success throughout Europe.
In Switzerland, Nomos established a prominent showcase in autumn 2010 – a flagship store in the centre of Zürich. That is not a bad address from which to carry the name of Glashütte out into the world. It means that time at Nomos and A. Lange&Söhne is likely to keep ticking for years to come.