How the cement and steel industries are reducing their CO2 emissions
Germany wants to become climate neutral by 2045 – innovative concepts in energy-intensive sectors are helping to achieve this goal.
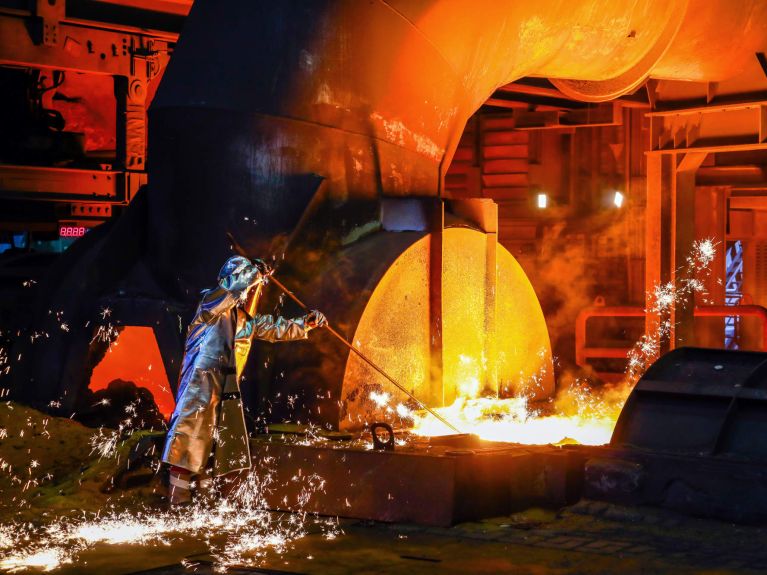
Many branches of industry require very large amounts of energy – which doesn’t make the fight against climate change any easier. Nonetheless, German industry is complying with the Federal Climate Change Act, which lays down the path to climate neutrality by 2045. Two examples of how particularly large polluters are achieving their targets:
Green concrete – Heidelberg Materials
After water, concrete is the world’s most widely used resource. During the production process,large amounts of CO2 are released, accounting for roughly eight percent of the world’s total carbon emissions. All the same, the industry plans to become climate neutral in Germany by 2045. It will do so by capturing, storing or utilising the carbon dioxide. With 51,000 employees and sales of 21 billion euros, Heidelberg Materials (formerly Heidelberg Zement) is one of the world’s largest cement manufacturers. The company is in the process of setting up a production facility in Norway at which the CO2 can be completely captured and later stored. “This will already enable us to produce the world’s first certified fully decarbonised cement by 2025 - which nobody else has managed to do as yet,” CEO Dominik von Achten said in an interview.
Green steel – Thyssenkrupp
One of the biggest steel manufacturers in the world, with 96,000 employees, is the Essen-based company Thyssenkrupp. The company has a clear goal for its global activities: “We want to be climate neutral by 2050 at the latest, significantly sooner in certain business segments and countries.” With their huge energy demand, steelworks are the biggest industrial carbon emitters – generating more emissions than the chemicals and cement industry combined. The steel industry is pinning its hopes on green energy: climate-neutral hydrogen and electricity. This should already enable emissions to be reduced by 30 percent by 2030, says the German Steel Association. Thyssenkrupp is following some innovative approaches to achieve this. In just a few years, the new tkH2Steel plant in Duisburg will already be producing “premium steel with green electricity and hydrogen in a direct reduction plant – rather than in a coal-fired furnace,” says the company.